Pump Station Efficiency
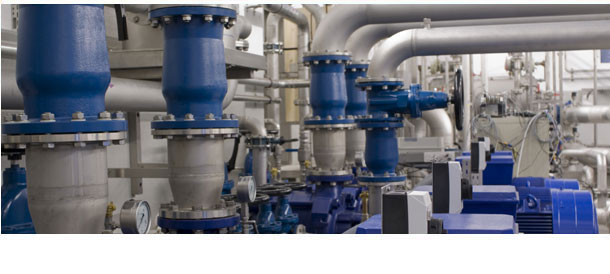
Our client was looking to improve the efficiency of its water pump sets. By programming a simple algorithm, we were able to establish an online monitoring system which cycles through the pump sets and triggers an alarm when efficiencies fall below an acceptable level.
From experience, we have found that most pump stations are equipped with enough measurement instrumentation to make calculating the pump efficiency possible. Therefore, it is a relatively simple process for any business to achieve power savings by monitoring pump efficiency.
We knew that we could achieve savings for our client as they had the tools there already.
Most water pump stations consist of the following elements:
- A supply reservoir where water is sourced from
- Pumps to pump water to a higher level
- A delivery pressure gauge
- A delivery flow meter
- Power monitoring on the pump station (optional)
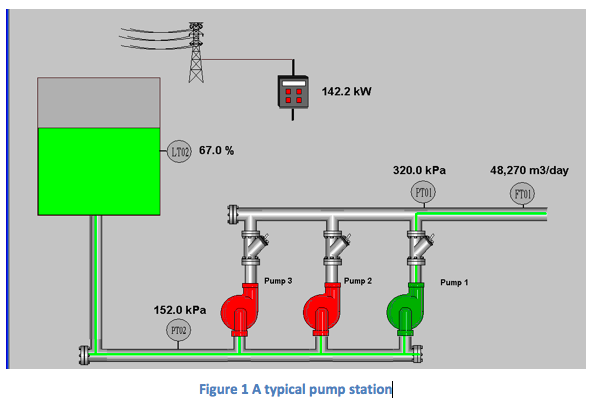
Often, only one pump is running at a time. So, the flow, pressure across the pumps and power consumed in the pump station can all be assigned to a particular active pump. Therefore, we can calculate the efficiency of the pump running at the time.
The combined mechanical and electrical efficiency of a pump set is a simple calculation.
Most pump stations also cycle the duty of each pump, which gives us an opportunity to calculate the relative efficiency of each pump in comparison with the others. So, if there are three pumps in a pump station and their duties cycle once per day, you will understand the efficiency of each by the end of the three days.
These were the results we found when we first tested the pumps:
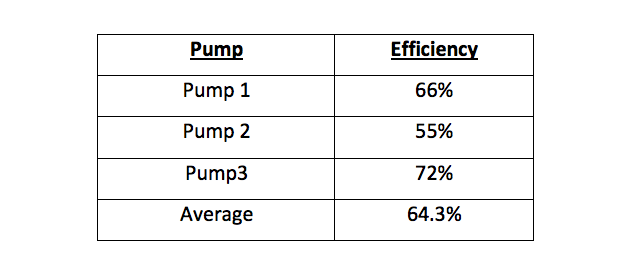
One of the many advantages of online efficiency monitoring is that worn or defective pump sets can be identified. From the information we gathered for our client, we found that Pump 2 had a much lower efficiency than the other two pumps.
We can also see that running Pump 3 most of the time can increase the average efficiency by 7%. On a pump set of 630kW that is a whopping 44 kW reduction in power. We achieved this by programming the system with an algorithm that utilises Pump 3 more than the others.
We also ensured that all efficiencies were logged into a historical database and an alarm would be generated when the efficiency drops below acceptable levels.
It didn’t take long for this system to pay off. It saved the day for our client when the outlet valve of a pump wasn’t shut due to a valve defect. Water was recirculating through that pump while another pump was running. Because of the online efficiency monitoring, an alarm was triggered as soon as the efficiency of the running pump dropped and the overall result for our client has been a 4% power saving achieved in a relatively short time.
Without the alarm, this situation may have continued for several months until routine maintenance caught up with the fault.
All in all, we have managed to create greater efficiencies for the client so that their plant runs better and saves them money!