Biogas Engine Optimisation
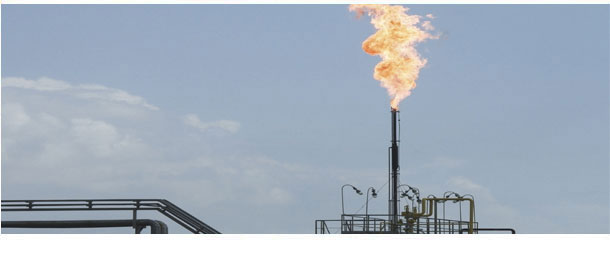
Our client was looking to optimise the performance of its biogas engines. The objective was to reduce natural gas use and biogas flaring and reduce the instances of engine tripping. The desired result was that the biogas engines can be run automatically, requiring less operational personnel. They wanted the only interruptions to be as a result of natural gas supply constraints, not system faults. They also wanted maintenance schedules with positive cost benefits.
A full version of this case study including diagrams can be downloaded here.
Our client wanted us to examine and optimise the control system of their biogas engines, fixing the instability of the current system. More often than not the client would run the process manually – causing excessive gas flaring or tripping of the engines due to gas starvation. Our objective was to reduce both natural gas usage and biogas flaring, resulting in a reduction of engine tripping instances. The result would create a positive cost-benefit and less effort required by operational personnel to run equipment.
The problems our client was having stemmed from rapid and uncontrollable fluctuation in the low-pressure gas holder. This was a major symptom caused by the blowers ramping up or down, engines starting and stopping, and variability in biogas production.
At startup, the control of the blower pressure would ramp up to 80% and a second blower would start at the same output percentage as the first. Almost twice the amount of gas would be transferred from the low pressure to the high-pressure gas side causing a sudden and drastic drop in the low-pressure gas holder level.
Their engine biogas blending control was based on trying to maintain a set level in the low-pressure gas holder. This strategy completely ignored the variation in biogas production and biogas supply pressure.
The sheer number of variations and combinations of equipment in this complex operation also caused problems. Each permutation and combination had a different open loop transfer function so a control strategy had to be designed to overcome this. Plus, the equipment was often left in ‘manual’ operation which meant unnecessary flaring of biogas.
Optimising the control system for the biogas engines had two goals:
Process stability – To get the engines running in ‘auto’, reduce the trips and start-ups, and
Process optimisation – Once the process was stable we could minimise biogas flaring and natural gas usage.
We automated the processes, implemented a number of controls to correct imbalances, programmed algorithms into the system and fixed discrepancies. The effect was a 66% reduction in tripping instances.
The end result means the engines are now left in automatic control. Trips of blowers or engines rarely occur, and engines hardly ever stop. Usually, a stop is because of natural gas supply contract constraints or for maintenance reasons.
Our client is now incredibly grateful to have a system with very little downtime, a low number of errors and is optimised to perform at maximum efficiency.